In the realm of high-precision printing, intaglio printing machines stand out as a cornerstone technology, particularly for applications that demand exceptional detail, durability, and security. From currency printing to high-end packaging and artwork reproduction, intaglio printing continues to evolve, powered by modern innovations and precision engineering.
Intaglio printing, a technique that originated centuries ago, involves engraving or etching an image into a metal plate. Ink is applied to fill the recessed areas, and the excess is wiped off the surface. Under high pressure, the image is then transferred to the paper or substrate, resulting in raised ink lines and deep texture that can be both seen and felt. This method not only produces stunning visual quality but also offers a level of anti-counterfeiting that is unmatched by other printing technologies.
In recent years, intaglio printing machines have undergone significant technological advancement. Automation, computer-controlled systems, and real-time error correction mechanisms have brought about substantial improvements in print quality, efficiency, and material adaptability. Advanced tension control, automated plate changing, and ink viscosity monitoring are now standard features in modern machines.
As global demand for secure printing grows, manufacturers in Asia—particularly China—have risen as leaders in the development and production of intaglio printing systems. Among them, one innovation has gained particular recognition: The most powerful intaglio printing machine in China. This cutting-edge machine integrates high-speed operation with ultra-fine engraving precision, supporting multiple ink systems and a wide range of materials. It represents the pinnacle of Chinese engineering and has begun to set new global benchmarks in the intaglio printing sector.
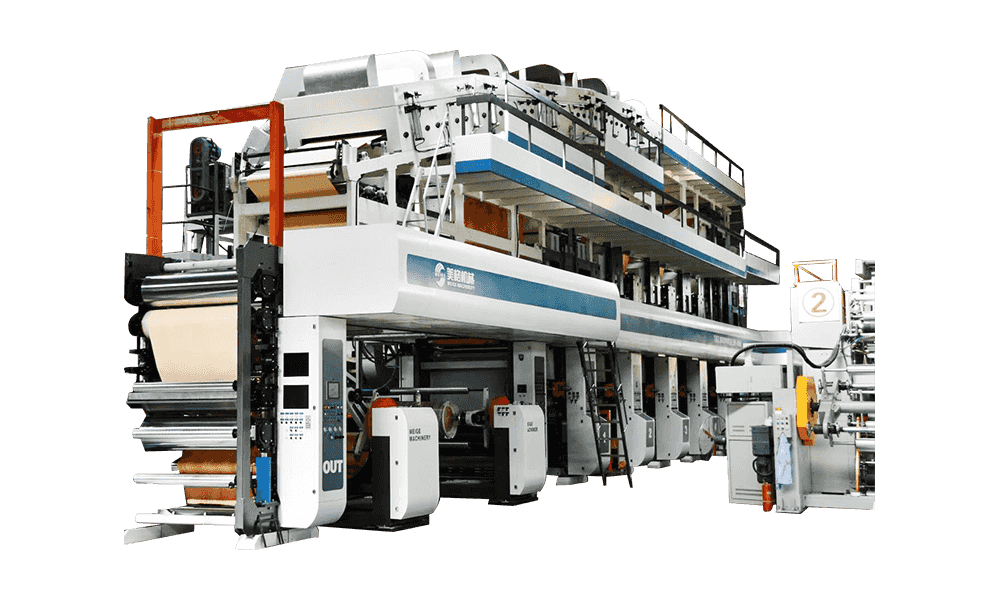
What makes this machine stand out is not just its power and precision, but also its adaptability to future needs. It is equipped with modular configurations, allowing users to upgrade components like ink stations, dryers, and inspection units. With a user-friendly interface and AI-driven diagnostics, operators can manage complex jobs with ease, minimizing downtime and maximizing output quality.
Moreover, environmental considerations are playing a growing role in the evolution of intaglio technology. Water-based inks, solvent recovery systems, and energy-efficient drying units are being implemented to reduce the ecological footprint of printing operations. The leading machines are now capable of maintaining high production speeds while adhering to strict environmental standards, making them suitable for global markets with stringent sustainability requirements.
The applications of intaglio printing machines are expanding beyond traditional industries. Today, they are being used in the production of luxury product packaging, security labels, fine art prints, and even in the electronics sector for micro-pattern printing. Their ability to deliver tactile and visually rich results makes them invaluable in industries where branding and authenticity are critical.