Rotogravure printing, often simply called gravure, is a high-quality intaglio printing process renowned for its exceptional image reproduction, vibrant colors, and consistency, particularly on demanding substrates like flexible packaging films and decorative laminates. The heart of this process lies within the intricate design and function of the rotogravure printing machine. Understanding its key components is essential to appreciating the precision and complexity involved.
1. Engraved Cylinder (The Core)
At the very heart of the rotogravure machine is the engraved cylinder. Unlike other printing methods that use raised or flat surfaces, gravure cylinders feature microscopic cells or wells etched into their surface. These cells vary in depth and/or size, dictating the amount of ink they hold, which in turn controls the density of the printed image.
-
Substrate: Typically steel, plated with copper for engraving, and then often chrome-plated for durability and wear resistance during the print run.
-
Engraving Methods: Cells are created using electromechanical engraving (diamond stylus), laser engraving, or chemical etching. The quality and consistency of these cells are paramount for print fidelity.
-
Ink Transfer: During printing, these cells pick up ink, and then transfer it directly to the substrate under pressure.
2. Ink Fountain and Doctor Blade System
This system is responsible for supplying ink to the engraved cylinder and removing excess ink from its non-image areas.
-
Ink Fountain: A reservoir that holds the gravure ink, which is typically solvent-based and low viscosity. The cylinder rotates through this fountain, picking up ink in its engraved cells.
-
Doctor Blade: A thin, flexible steel blade that rests against the rotating engraved cylinder. Its crucial role is to wipe away all the excess ink from the non-engraved, smooth surface of the cylinder, leaving ink only within the cells. The angle, pressure, and oscillation of the doctor blade are critical for clean and consistent printing.
3. Impression Roller
Positioned directly above the engraved cylinder, the impression roller applies pressure to the substrate, forcing it into contact with the inked cells of the engraved cylinder.
-
Material: Typically a rubber-covered roller, often with a harder rubber durometer to ensure even pressure distribution.
-
Function: The pressure from the impression roller ensures that the substrate picks up nearly all the ink from the engraved cells, resulting in a sharp and dense image. Without adequate and consistent impression, ink transfer would be poor.
4. Unwind and Rewind Units
These units manage the continuous web of substrate as it moves through the printing process.
-
Unwind Unit: Holds the roll of unprinted substrate and unwinds it at a controlled tension. Sophisticated tension control systems are crucial to prevent wrinkles, stretching, or misregistration.
-
Rewind Unit: After printing and drying, this unit rewinds the printed substrate into a finished roll, again maintaining precise tension.
5. Drying Systems
Gravure inks are typically solvent-based and dry very rapidly through evaporation. Therefore, efficient drying systems are vital after each color station.
-
Drying Chambers/Ovens: Each print unit is followed by a drying system, usually an enclosed chamber where heated air is circulated over the newly printed web.
-
Exhaust Systems: Crucial for safely removing solvent vapors, often with solvent recovery or incineration systems for environmental compliance and safety.
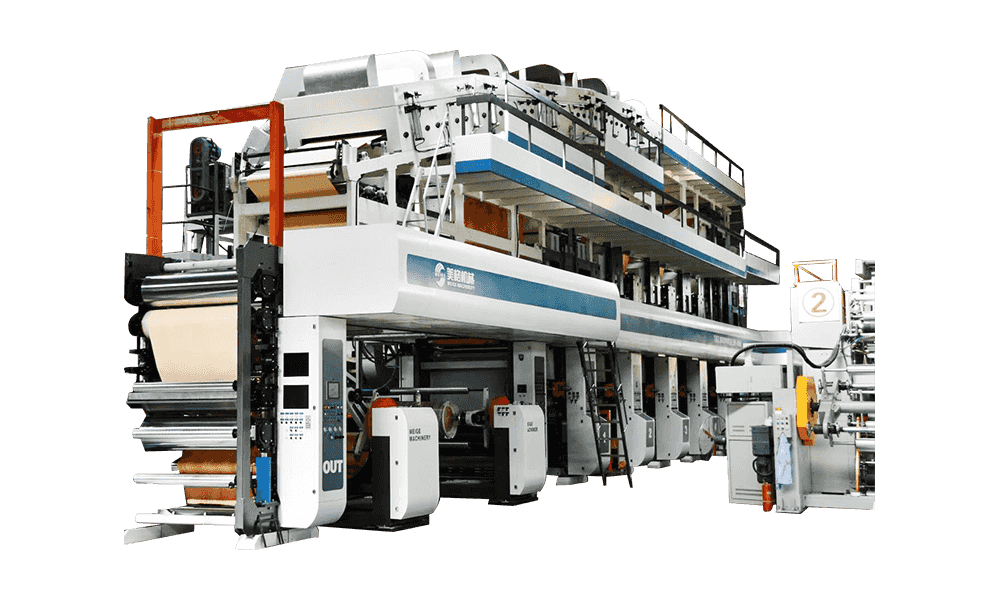
6. Register Control System
For multi-color printing, maintaining precise register (the accurate alignment of each subsequent color) is paramount.
-
Sensors: Optical sensors read small registration marks printed on the web.
-
Actuators: These sensors feed data to a control system that then makes minute adjustments to the web tension or cylinder position to ensure perfect alignment of each color, preventing blurry or misaligned images.
7. Inking and Circulation System
Beyond the fountain, a complete inking system ensures consistent ink quality.
-
Pumps: Circulate ink from a main reservoir to the ink fountain and back.
-
Viscosity Control: Gravure ink viscosity is critical for consistent print quality. Automated systems often monitor and adjust ink viscosity by adding solvents as needed.
-
Filtration: Filters remove impurities and agglomerates from the ink.
8. Web Guiding System
As the substrate moves at high speeds, web guiding systems prevent lateral movement and ensure it remains perfectly centered through the machine.
9. Control Panel and Automation
Modern rotogravure machines are highly automated, controlled by sophisticated computer systems.
-
Human-Machine Interface (HMI): A central control panel allows operators to monitor and adjust various parameters, including speed, tension, temperature, ink viscosity, and register.
-
Diagnostics: Advanced systems provide real-time diagnostics and fault finding.
The harmonious interaction of these components enables rotogravure printing machines to produce the high-quality, durable, and aesthetically pleasing prints that are a hallmark of the process. From the microscopic precision of the engraved cylinder to the intricate dance of tension and registration, each part plays an indispensable role in delivering superior results for a wide range of applications.